Fusing Properties
&
Torch/Hose Connections
We have lots of “new members” so we invite the new members as well as those who have been in the club for a while or forever, and who have great ideas, to send them to tipsandtricks@theglassdragons.com. We would love to hear what you do that can help others.
~ Beverly Seibenhener
Torch Connections:
Janie Jones shared the following tips:
- Never use oil products on hose connections or the safety cap on tanks. Rub a bar of soap on the threads for easy connect/disconnect.
- Test for hose leaks by applying a mix of liquid dish wash & water to joints – bubbles show up if there is any oxy or propane leaking.
For the glass fusers in our midst:
Delphi Glass offers the following tips for understanding the properties of Hot Glass:
When heating glass to a full fuse (1450° F) it wants to become ¼” or 6mm thick and round. A standard sheet of glass is approximately 1/8″ or 3mm thick.
When firing a single layer of glass the edges will contract to become ¼” thick.
If fusing three layers of glass your glass will expand to become ¼” thick.
Unless you are damming the glass, two layers are ideal to maintain your project’s original size and general shape.
In the picture below, notice how the following stacks of glass appear before and after firing.

In the next picture, notice how each cabochon is approximately the same thickness (6mm).

Viewing the cabochons from the top you can see how the stacks spread when they were fired.
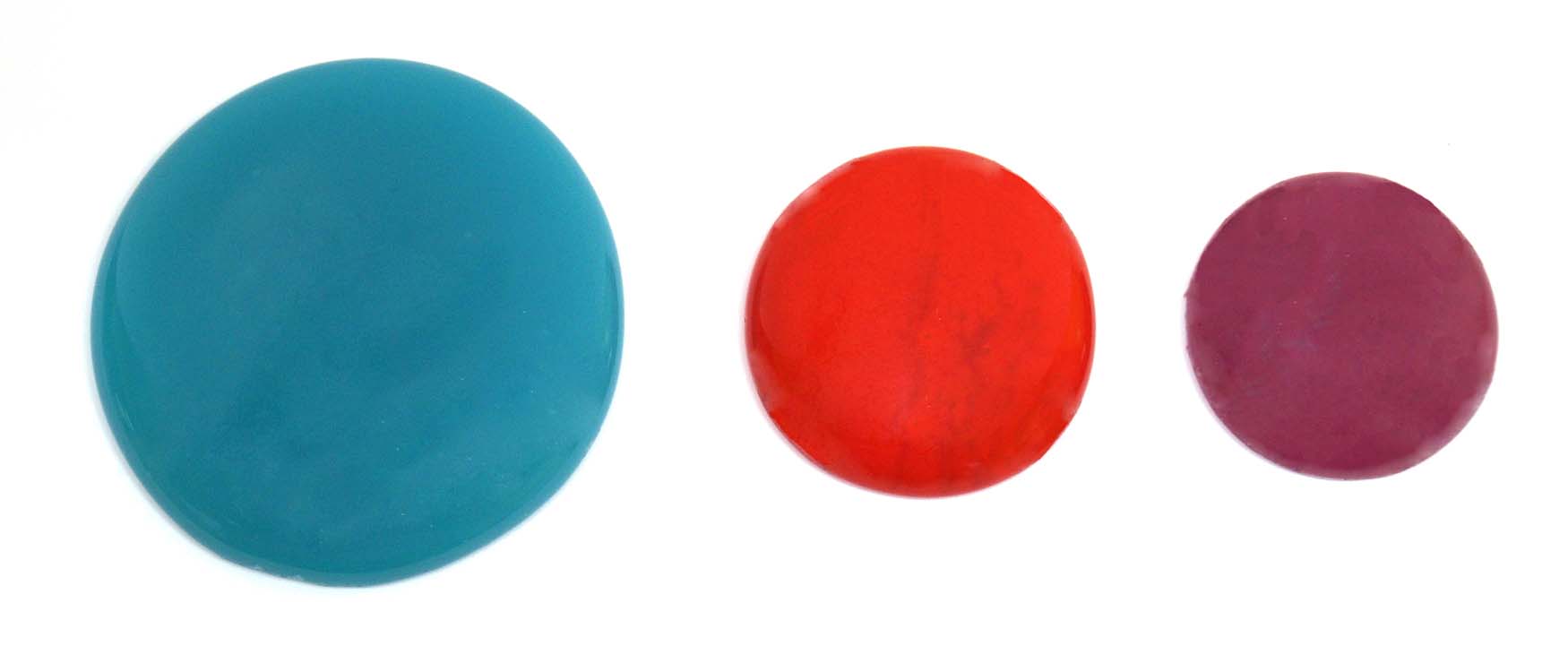
Keeping the ¼” rule in mind will help you achieve your desired effect, hopefully, without growing or shrinking your project unintentionally.